Get Knowledgeable About The Round Bar Manufacturing Process
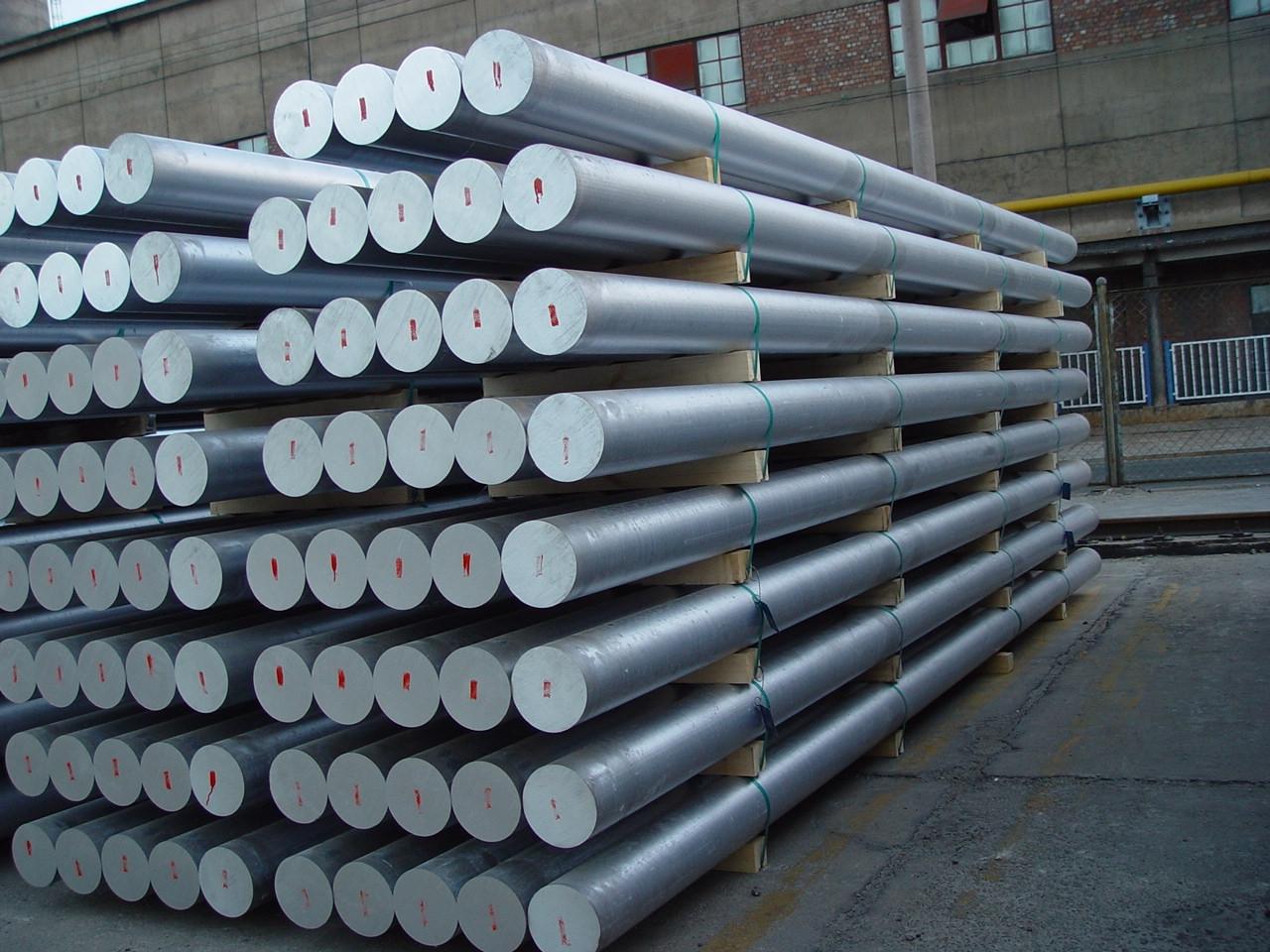
As one of the widely used and highly popular metal, steel has been around since ancient times. However, the widespread use and utilization of this robust, unique, and strong metal have begun quite recently. From heavy engineering to construction, steel has emerged as the most effective metal used in diverse industrial sectors.
Diverse industries require steel for a multitude of purposes. Quite naturally, that creates the demand for various steel products. From steel bars to wires and coils, you will come across a gamut of products in the market.
With a variety of applications, round-steel bars rank amongst the top steel products. Developed and manufactured through an intricate process, these steel bars are durable and long-lasting. Breeze through the following article, as it explains the round steel bar manufacturing process.
Breaking down the processes
Round steel bar manufacturing encompasses quite a few aspects. From the collection of raw materials to processing and inspection, numerous processes are involved in it. Let’s understand these individual methods in a comprehensive manner.
1. Raw material collection
Raw and unprocessed steel is collected through proper collection process. After this collection, the metal undergoes testing.
2. Chemical and Physical Testing
Targeted and proper testing become highly imperative in the steel manufacturing and production process. Once the collection process is over, testing emerges as the next significant process. Steel production units will perform both physical and chemical testing, thus checking the durability of the raw materials.
3. Heating
The next important process is heating. Steel bars undergo pressure heating followed by the rolling processes. Under this process, manufacturers can improve the ductility of the steel bars.
4. Hot rolling
Round bars have to be rolled into the appropriate shape. After continuous heating, it is the hot rolling procedure that helps the raw steel acquire the desired shape. The process is highly important for steel production.
5. Inspection
After the successful completion of the hot rolling process, manufacturers need to perform targeted inspection. It is after this inspection that manufacturers get assured of bar quality.
6. Water quenching in controlled environments
Performed right after inspection, the water-quenching procedure happens to be of huge significance. By using patented thermex systems, experts perform water quenching under controlled conditions.
7. Hot inspection
The inspection process takes place again for checking the condition of the final product. Hot inspection helps you know about the performance and resistance standards of the round bars.
8. Physical Testing
Since round bars find widespread use and application in various construction processes, it becomes imperative to check its strength and durability. Reliable and world-class manufacturers perform a final physical testing process, thus reassuring the grade and performance of these bars.
9. Dispatch
After the penultimate process, it’s time for the final phase. Round bars get packed and dispatched. Once they reach the market, construction engineers, and manufacturing plant owners can buy them.
Accurate execution of processes
There is no denying the fact that all these processes are highly necessary for proper production and manufacture of round bars. And only the most proficient and reliable manufacturers can perform it with utmost finesse and precision.